7 Reasons Why Manufacturing Needs PLC Programming for Efficiency
- June 24, 2024
- Posted by: Ashish Dayma
- Category: Knowledge Hub
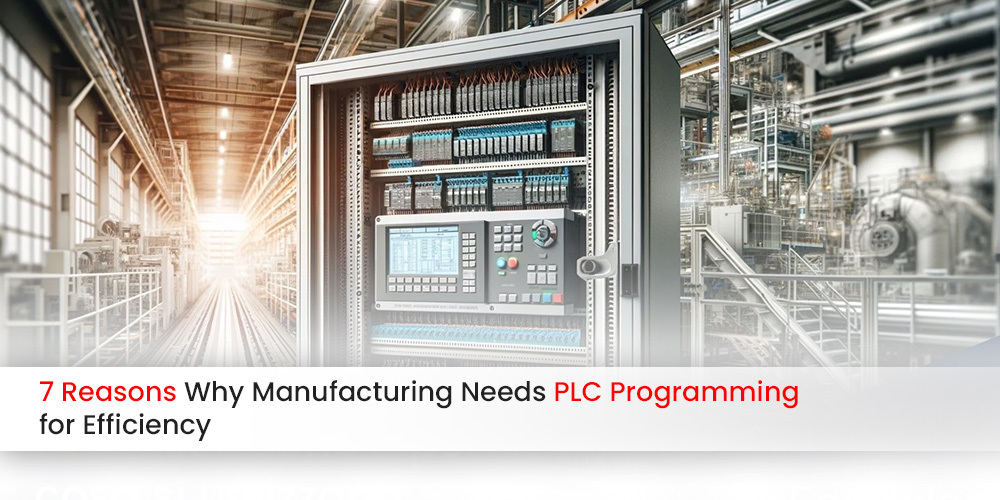
In today’s competitive manufacturing landscape, efficiency reigns supreme. Every second counts, every unit produced matters, and any downtime can spell disaster. This is where Programmable Logic Controllers (PLCs) step in, offering a powerful and versatile solution for streamlining and optimizing manufacturing processes.
PLCs are essentially industrial computers designed to automate complex tasks and control machinery on the factory floor. By replacing traditional relay logic and manual control systems, PLCs offer a multitude of benefits that translate directly to increased efficiency. Here are seven compelling reasons why manufacturing needs PLC programming to stay ahead of the curve:
Enhanced Productivity and Throughput:
PLCs excel at automating repetitive tasks, freeing up human operators for more strategic roles. Imagine an assembly line where a PLC flawlessly handles robotic arm movements, conveyor belt timing, and product sorting – all based on pre-programmed instructions. This translates to faster production cycles, increased output, and the ability to meet higher demands without additional manpower.
- Reduced Downtime and Improved Uptime:
Manufacturing thrives on consistent operation. PLCs can be programmed to monitor equipment health and performance in real-time. They can detect potential issues like overheating motors or malfunctioning sensors before they cause a complete breakdown. This allows for preventive maintenance, reducing the likelihood of unplanned downtime and ensuring smooth operation for extended periods.
- Improved Accuracy and Consistency:
Human error is an inevitable part of any manual process. PLCs, on the other hand, operate with unwavering precision. Once programmed, they consistently execute instructions flawlessly, ensuring consistent product quality and eliminating the risk of human error affecting crucial steps in the production process.
- Increased Flexibility and Scalability:
Manufacturing needs often evolve, and traditional control systems can be inflexible and difficult to modify. PLCs offer exceptional adaptability. Their programs can be easily edited and updated to accommodate changes in production lines, product designs, or operational requirements. Additionally, PLCs can be easily scaled to accommodate future growth. Adding new equipment or expanding production lines simply involves integrating them into the existing PLC program.
- Optimized Resource Management and Energy Efficiency:
PLCs can be programmed to optimize resource usage. They can control parameters like motor speed, lighting levels, and compressed air usage based on real-time needs. Additionally, PLCs can be integrated with energy monitoring systems, allowing for data-driven adjustments to further reduce energy consumption in your manufacturing facility.
- Improved Data Acquisition and Process Analysis:
Modern PLCs are equipped with sophisticated data logging capabilities. They can collect and store valuable data on production parameters, equipment performance, and product quality. This data can be analyzed to identify bottlenecks, optimize processes, and make informed decisions to further enhance efficiency.
- Enhanced Safety and Improved Work Environment:
PLCs play a crucial role in maintaining a safe work environment. They can be programmed to implement safety protocols like emergency shutdowns in case of equipment malfunction or hazardous situations. Additionally, by automating dangerous or repetitive tasks, PLCs can minimize the risk of operator injuries, fostering a safer work environment for your employees.
Unlocking the Power of PLC Programming at iPacAutomation:
Here at iPacAutomationhttps://ipacautomation.com/, we understand the transformative power of PLC programming in manufacturing. We offer a comprehensive range of services, including:
- PLC programming and system design:Our expert engineers can design and develop customized PLC programs tailored to your specific manufacturing needs.
- PLC training and certification:We provide a variety of training programs to equip your team with the skills and knowledge to program, maintain, and troubleshoot PLC systems.
- PLC troubleshooting and maintenance:Our team offers expert support to diagnose and resolve PLC-related issues, ensuring optimal uptime for your production lines.
Conclusion:
By embracingPLC programming, manufacturers can unlock a new level of efficiency, productivity, and safety. With their versatility, adaptability, and data-driven capabilities, PLCs offer a compelling solution for optimizing your operations and propelling your manufacturing success in the years to come.
Take the first step towards a more efficient future by contacting iPacAutomation today. Let us help you harness the power of PLC programmingand transform your manufacturing processes!