The landscape of manufacturing is undergoing a significant transformation.Industrial automation, the integration of advanced technologies like robots, machine learning, and data analytics, is rapidly changing how products are designed, produced, and delivered. While concerns about job displacement are natural, the reality is that industrial automation is not rendering the human workforce obsolete. Instead, it’s reshaping it, creating new opportunities and demanding a new skillset from modern manufacturing professionals.
The Rise of Automation and Its Benefits
The rise of automation in manufacturing is driven by several factors, including:
- Increased Efficiency and Productivity: Automated systems can perform tasks faster and more consistently than humans, leading to higher production rates and reduced waste.
- Improved Quality Control: Automation minimizes human error, resulting in more consistent product quality and fewer defects.
- Enhanced Worker Safety: Repetitive and potentially hazardous tasks can be safely handled by robots, reducing workplace injuries.
- Reduced Labor Costs: While there is an initial investment in automation technology, it can lead to long-term cost savings through increased efficiency and reduced labor needs.
The Evolving Role of Human Workers
With automation taking over repetitive tasks, the role of human workers in manufacturing is shifting towards:
- Technical Expertise: Operating, maintaining, and troubleshooting complex automated systems requires a strong understanding of robotics, programming, and data analysis.
- Problem-solving and Critical Thinking: Workers will need to identify and address unexpected issues, optimize processes, and continuously improve systems for efficiency.
- Data Management and Analytics: Interpreting data from sensors and control systems will be crucial for optimizing production and predicting potential problems.
- Collaboration and Teamwork: Human-machine collaboration is becoming increasingly important. Workers will need to effectively communicate with their robot colleagues and manage teams with diverse skillsets.
- Project Management and Leadership: As automation becomes more complex, overseeing projects, ensuring smooth integration of systems, and leading teams of specialists will be vital.
The Future of Manufacturing Jobs
The Bureau of Labor Statistics predicts that while some manufacturing jobs will decline, others will grow significantly. New positions will emerge in areas like automation engineering, robotics technicians, data analysts, and cybersecurity specialists. The key is for workers to adapt and develop the necessary skills to thrive in this evolving environment.
How Can Manufacturers Prepare Their Workforce?
Manufacturing companies can proactively prepare their workforce for the future by:
- Investing in Skills Development: Provide training programs on automation technologies, data analysis, and project management.
- Promoting Upskilling and Reskilling: Offer opportunities for current employees to learn new skills and transition to new roles within the company.
- Building a Culture of Continuous Learning: Encourage ongoing learning and knowledge sharing to stay updated with the latest advancements.
- Attracting New Talent: Highlight the exciting opportunities and new skillsets required in a modern, automated manufacturing environment.
Benefits of a Skilled Workforce in an Automated Environment
A skilled and adaptable workforce is critical for maximizing the benefits of automation. Here’s how:
- Faster Integration and Implementation: A skilled workforce can quickly learn and adapt to new technologies, leading to faster and more efficient integration of automation solutions.
- Optimizing Automation Systems: With a deep understanding of both automation and manufacturing processes, workers can continually optimize systems for maximum efficiency and productivity.
- Innovation and Problem-Solving: A skilled workforce can identify new ways to utilize automation, troubleshoot complex issues, and drive further innovation within the manufacturing process.
- Maintaining High-Quality Standards: Skilled workers can ensure automation systems are configured and maintained to produce high-quality products consistently.
Conclusion: A Bright Future for Manufacturing with Human-Machine Collaboration
Industrial automation is undoubtedly transforming the manufacturing workforce. However, this is not a story of machines replacing humans. It’s a story of humans and machines working together in a collaborative environment. By embracing automation and investing in their workforce, manufacturers can create a future of increased productivity, improved quality, and a more rewarding and safe work environment for their employees.
For a comprehensive range of industrial automation services, including consulting, engineering, and implementation, visit IPAC Automation atIPAC Automation Services. We can help you leverage the power of automation to optimize your manufacturing processes and build a future-proof workforce.
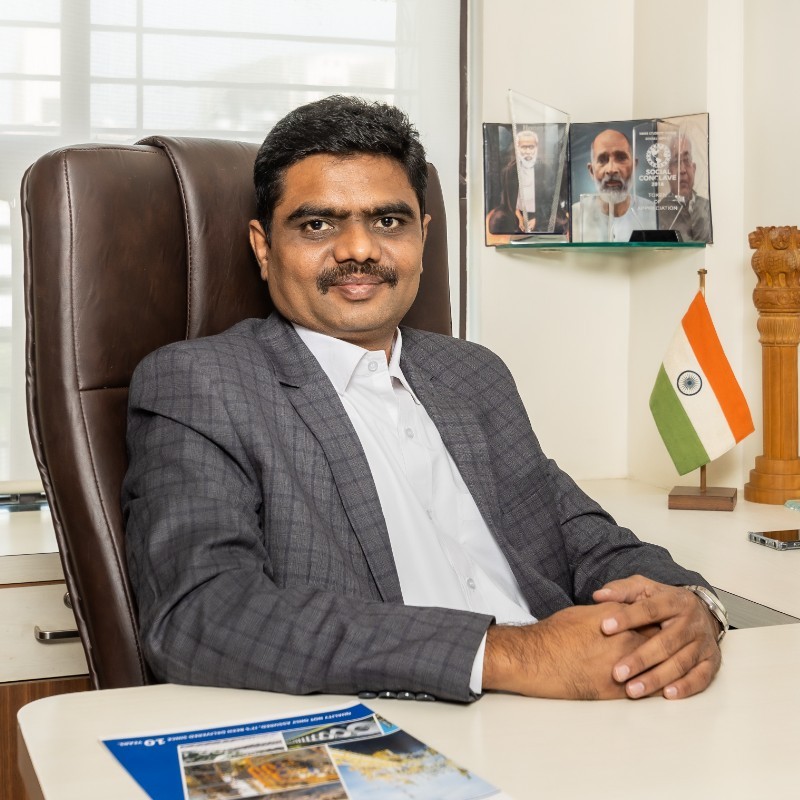
Waman Sanap is the CEO of iPAC Automation, a leading instrumentation and control automation company. He has 20+ years of experience in the instrumentation engineering field.