Key Considerations in PLC Programming for Modern Industrial Automation
- October 22, 2024
- Posted by: vishal pharos
- Category: Uncategorized
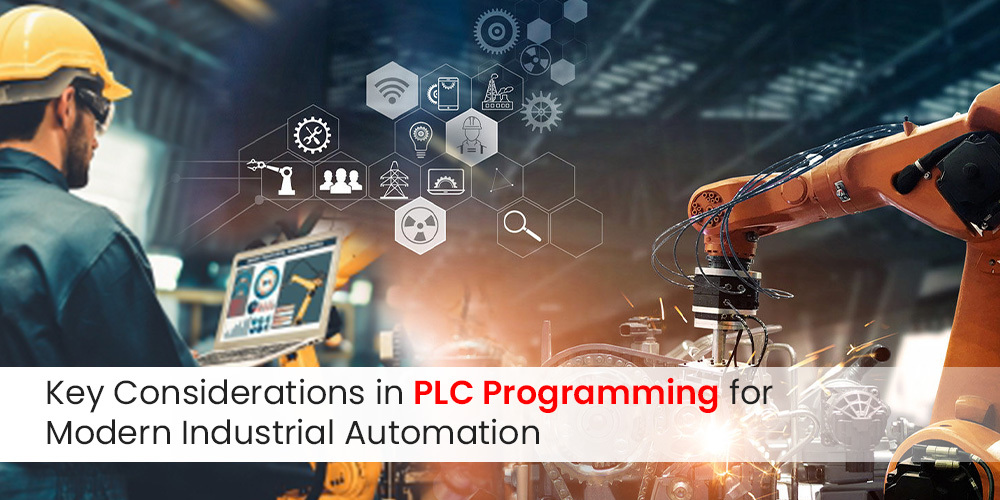
As industrial processes grow increasingly complex and competitive, PLC programming has become a cornerstone of modern industrial automation. The shift from legacy systems to more advanced platforms requires robust and flexible programming that can handle evolving operational demands. This blog will explore the key considerations in PLC programming to ensure efficiency, scalability, and safety, providing insights drawn from industry practices and IPAC Automation’s expertise.
Understanding the Importance of PLC Programming in Automation
PLC programming is essential for controlling automated industrial processes. These programs manage machinery and systems in real time, ensuring smooth operations by processing inputs from sensors and executing predefined tasks. As industries embrace digital transformation, the need for agile, scalable, and reliable PLC programming is greater than ever.
Key areas of focus in modern PLC programming include adaptability, precision, and integration with Distributed Control Systems (DCS). By aligning programming strategies with these requirements, businesses can achieve more efficient automation processes while minimizing downtime during control system upgrades or migrations.
Key Considerations in PLC Programming
1. Modularity and Scalability in Program Design
One of the fundamental principles in modern PLC programming is modular programming. Modular designs allow developers to break down large and complex programs into smaller, independent modules. This not only simplifies troubleshooting but also enhances scalability. Each module performs specific tasks, such as managing a motor or controlling temperature, which can easily be adjusted or expanded without impacting other parts of the system.
This approach is particularly useful when upgrading from legacy systems, as discussed in IPAC Automation’s PLC and DCS migration services. Modular PLC programs enable smoother transitions, ensuring that new functionalities can be added seamlessly without disrupting existing processes.
2. Customization for Industry-Specific Requirements
Every industry has unique operational demands, and PLC programming must be tailored to meet these specific needs. For example, in sectors like oil and gas, safety is paramount, and programming must prioritize reliable control of critical equipment. In the pharmaceutical industry, precision in data collection and process control is key to ensuring product quality.
IPAC Automation emphasizes customized programming solutions for clients across various industries. This means considering factors such as environmental conditions, operational parameters, and regulatory requirements while developing PLC code, ensuring that it aligns with both current and future needs.
3. Seamless Integration with Existing Systems
In many cases, PLC programming involves integrating new platforms with existing control systems, such as DCS. Successful integration requires programming flexibility, enabling seamless communication between legacy systems and modern PLCs. This is where IPAC’s expertise in data migration and system analysis plays a crucial role. The transition from old systems to new, advanced PLC programs needs to happen with minimal disruptions to ongoing operations.
Data integrity is another key consideration. Proper PLC programming ensures that all essential data is accurately transferred during migration, preventing errors or downtime.
4. Safety and Compliance with Standards
Safety is non-negotiable in industrial automation. When designing PLC programs, ensuring compliance with safety standards such as SIL (Safety Integrity Level) or IEC 61508 is critical. These standards outline the functional safety requirements that PLCs must meet, especially in industries where equipment failure could have severe consequences.
Redundancy is another programming consideration that helps prevent system failures. In the event that a primary system fails, backup systems, managed through PLC programming, can take over, ensuring continuous and safe operation. IPAC Automation offers tailored safety solutions by incorporating redundant control strategies into their PLC programs.
5. Future-Proofing for Technology Advancements
Industries are continually evolving, and so are the technologies they use. PLC programs must be designed with future expansion in mind. This means that programs should be adaptable to new technologies like IoT (Internet of Things), AI (Artificial Intelligence), and machine learning.
By incorporating flexible and scalable programming architectures, businesses can ensure that their systems remain relevant as technology advances. This future-proofing can reduce the need for frequent and costly reprogramming while keeping systems aligned with technological trends.
Conclusion
In the world of industrial automation, PLC programming plays a critical role in ensuring efficiency, safety, and adaptability. By considering modularity, customization, system integration, safety, and future-proofing, industries can optimize their automation systems to meet both current and future demands.
IPAC Automation’s expertise in PLC programming and DCS migration showcases the importance of designing reliable and scalable programs that improve process efficiency, minimize downtime, and ensure long-term system sustainability.