How Industrial Automation Minimizes Downtime and Maximizes Profits
- July 15, 2024
- Posted by: Ashish Dayma
- Category: Uncategorized
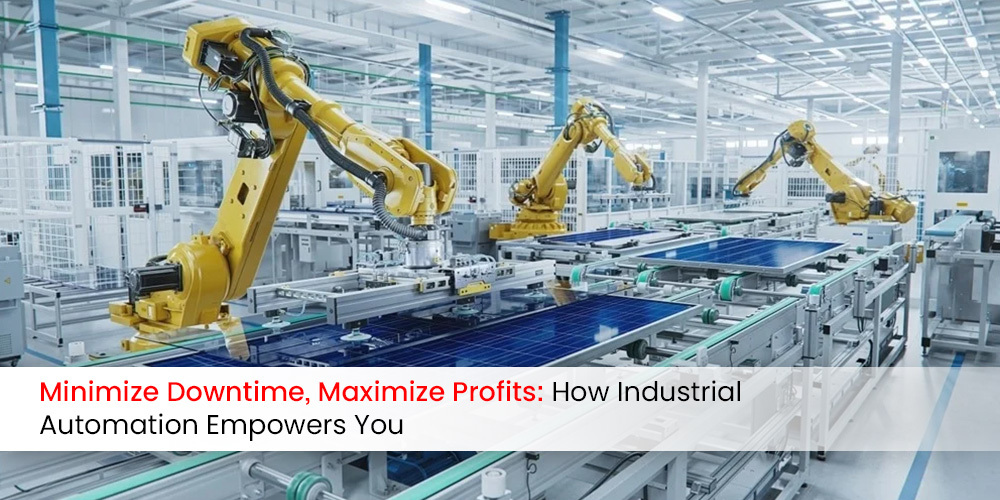
In today’s competitive manufacturing landscape, every minute of production downtime translates to lost revenue. Fortunately, industrial automation offers a powerful solution, minimizing disruptions and maximizing profitability. By automating repetitive tasks, improving process control, and facilitating predictive maintenance, industrial automation empowers businesses to achieve operational excellence.
The High Cost of Downtime
Unplanned downtime can be a significant financial burden. According to a study byIndustryWeek, unplanned downtime costs manufacturers an average of $50,000 per hour. These costs encompass lost production, wasted labor, and the additional expenses associated with expediting repairs. The impact extends beyond immediate financial losses, potentially damaging customer relationships due to delayed deliveries and unmet production targets.
Industrial Automation to the Rescue
Industrial automation steps in to combat these challenges by:
- Minimizing Human Error: Manual processes are inherently prone to human error, which can lead to equipment malfunctions and production stoppages. Industrial robots and automated machines perform tasks with consistent accuracy, reducing the likelihood of errors that cause downtime.
- Enhancing Process Control: Industrial automation systems integrate sensors and control systems, allowing for real-time monitoring and precise control of production processes. This enables adjustments to be made quickly in response to deviations, preventing problems before they escalate into major breakdowns.
- Predictive Maintenance: Advanced automation systems can collect and analyze data on equipment performance. By identifying subtle changes in operating parameters, these systems can predict potential issues before they cause failures. This allows for proactive maintenance, scheduling repairs during planned downtime to minimize disruption.
- Improved Equipment Utilization: Automation streamlines workflows, enabling continuous operation and maximizing the utilization of production equipment. This translates to increased output and a higher return on investment (ROI) for your automation systems.
Beyond Minimizing Downtime
The benefits of industrial automation extend beyond simply minimizing downtime. These systems also contribute to:
- Enhanced Product Quality: Automation ensures consistent product quality by eliminating human error and precisely controlling manufacturing processes. This leads to fewer defects, improved customer satisfaction, and a stronger brand reputation.
- Increased Productivity: By automating repetitive tasks, industrial systems free up human workers to focus on higher-value activities. This leads to a more efficient workforce and increased overall production output.
- Improved Safety: Automating hazardous tasks removes workers from potentially dangerous situations. This leads to a safer work environment and reduces the risk of workplace accidents.
- Reduced Labor Costs: While there may be initial investment costs associated with automation, the long-term benefits often outweigh the upfront expenses. Automation can significantly reduce labor costs by streamlining production processes and minimizing reliance on manual labor.
Building a Business Case for Automation
When considering industrial automation, it’s crucial to build a compelling business case to assess the potential ROI. Here are some key factors to consider:
- Identify Downtime Costs: Analyze historical data to quantify the financial impact of downtime at your facility. This will help you understand the potential financial gains from minimizing disruptions.
- Evaluate Current Processes: Identify bottlenecks and areas prone to human error within your production line. These areas are prime candidates for automation, as they offer the most significant potential for improvement.
- Define Automation Goals: Clearly outline your desired outcomes from implementing automation. This may include increased productivity, improved quality control, or reduced labor costs.
- Develop a Cost-Benefit Analysis: Evaluate the upfront investment costs of automation systems against the projected long-term benefits. Consider factors like increased output, reduced downtime, and improved efficiency.
Getting Started with Industrial Automation
IPAC Automationis your trusted partner in implementing industrial automation solutions. We offer a comprehensive range of services, from initial consultation and project planning to system design, installation, and ongoing support. Our team of experienced engineers will work closely with you to assess your specific needs and develop a customized automation solution that maximizes your profitability and minimizes downtime.
Embrace the Future of ManufacturingIndustrial automation is not just a technological advancement; it’s a strategic investment in the future of your business. By minimizing downtime, maximizing productivity, and enhancing overall efficiency, industrial automation empowers you to achieve a significant competitive advantage. Contact IPAC Automation today and discover how we can help you harness the power of industrial automation to unlock a new era of success for your manufacturing operations.