Selection of Correct RTDs For Your Sensing Application
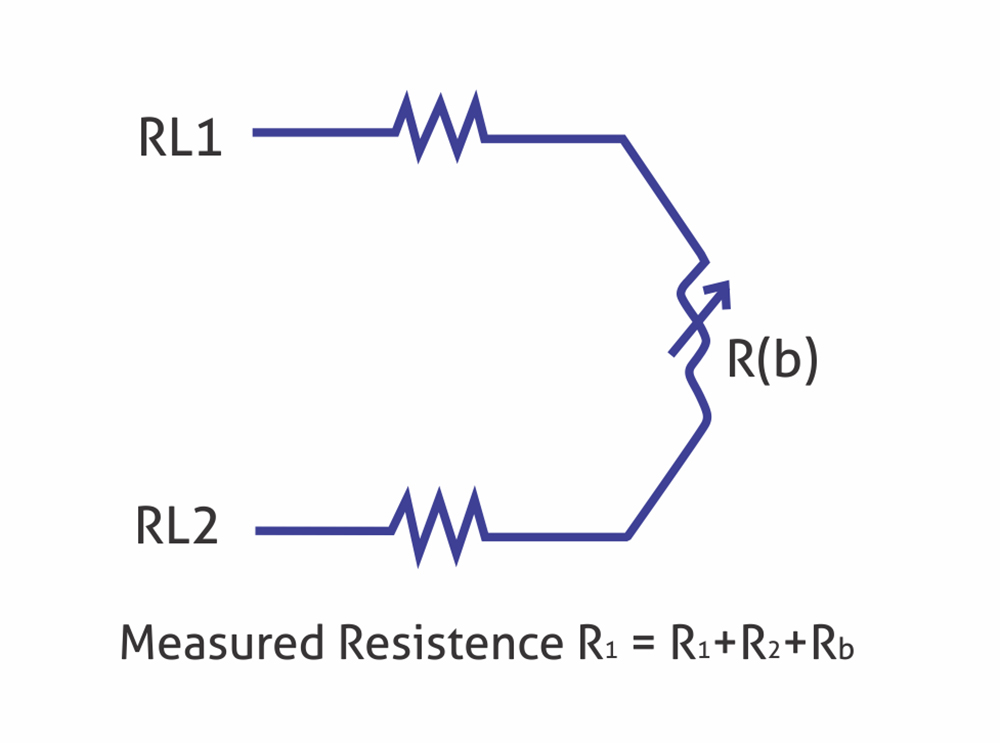
2 – Wire RTD
- Low accuracy
- Measurement errors
- Less expensive
- Connecting wires should not be lengthy
- Simplest circuit design
- A single lead wire connects to each end of the element
- The resistance in the circuit is calculated by measuring the resistance in the lead wires and connectors
- This results in some degree error or readout that is higher than the actual measured temperature. This can be eliminated with calibration

3 – wire RTD
- Better accuracy than 2 -wire
- Fewer errors
- Less expensive than the 4 wire
- The wires which are used should have the same length, Long connecting wires can be used
- The three wire configuration is the most used in industrial applications
- Two wires are connected to one end of the sensor, RL2 and RL3, and to the monitoring device. The third wire, RL1, is connected to the element
- The three wires are of equal length, so their resistance is equal
- The 2-wire configuration also has errors that have to be adjusted by calibration.
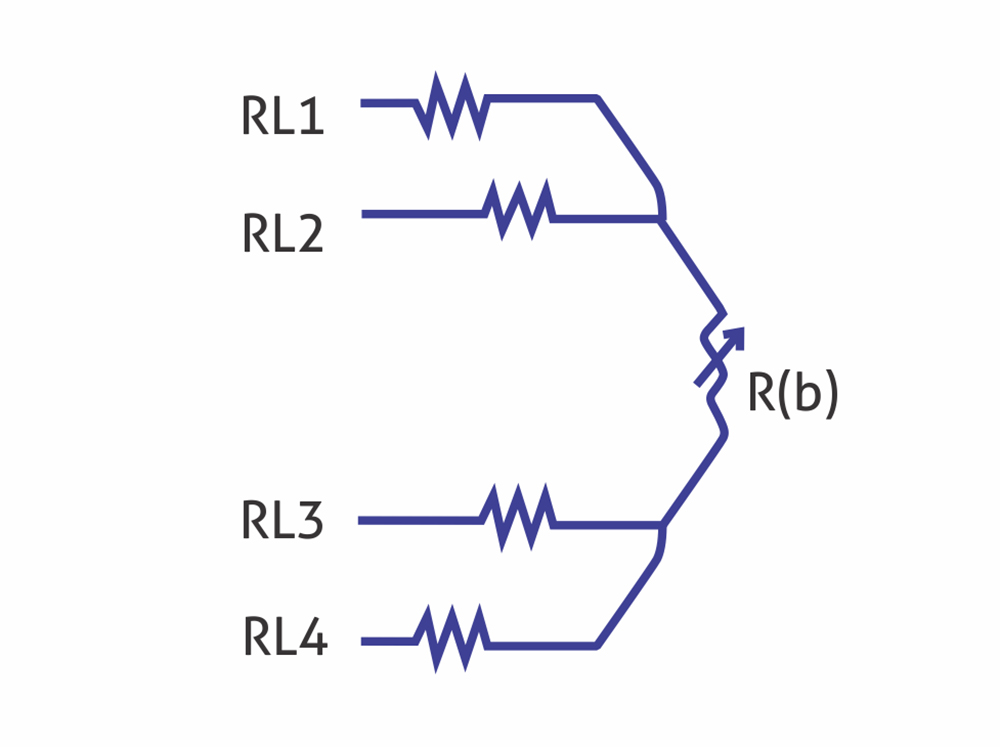
4- wire RTD
- High accuracy
- Won’t be any error
- Very expensive
- Long connecting wires can be used
- The four wire configuration is the most complex
- DC current is provided through two leads, RL1 and RL4. The voltage drop is measured by the other two leads, RL2 and RL3.
- The voltage drop and current are known, making the resistance easy to read as well as the temperature across the system.
- The 4-wire configuration is time consuming, and expensive to install but produces the most accurate and precise readings.
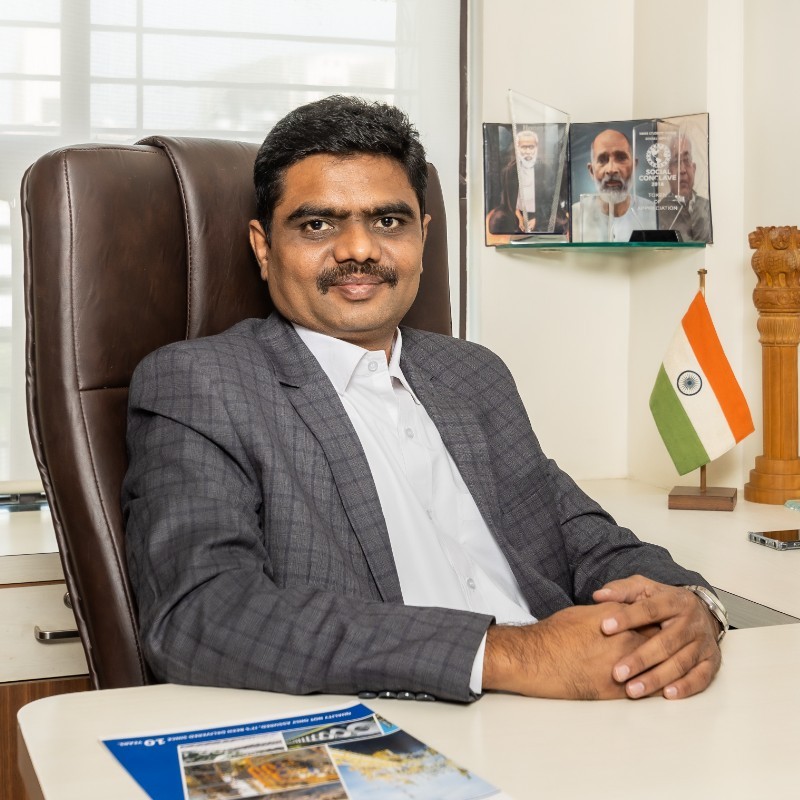
Waman Sanap is the CEO of iPAC Automation, a leading instrumentation and control automation company. He has 20+ years of experience in the instrumentation engineering field.