Power Generation Plant Control System Automation Project Details
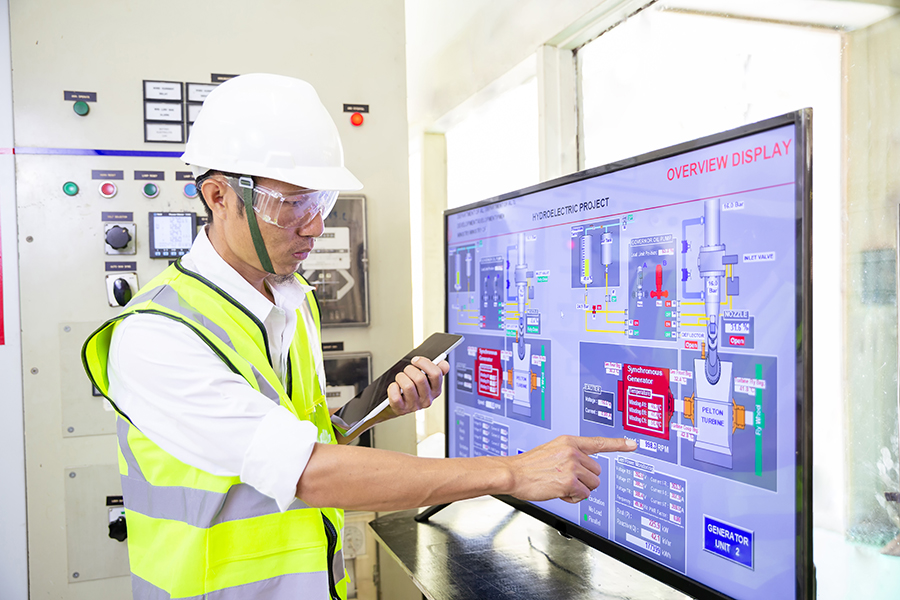
Scope of Work :
- Study of customer input.
- Preparing the IO assignment from the customer IO list.
- Installation of hardware like HC900 controller, AI,AO,DI,DO cards Installation.
- Logic development of HC900 controller in Hybrid Contol Designer.
- Hot and cold loop checking.
- Logic modification as per customer Comments.
- HMI Graphics modification as per customer requirement.
- Building the Channel, Controller and points in Quick Builder.
- Check the communication between logic and graphics.
- Communication of SCADA points of HC900 Controller through the Quick Builder(QDB).
Precision Control System Automation for Power Generation Plants
In the critical and dynamic realm of power generation, flawless control system automation is the bedrock of efficiency, reliability and safety. At iPAC Automation, a leading automation system integrator in Pune, Maharashtra, India, we deliver comprehensive, meticulously engineered solutions that transform your power plant operations. Our expertise spans the entire project lifecycle, from initial concept to effortless commissioning, ensuring your facility operates at its absolute best.
Is Your Power Plant’s Control System Delivering Optimal Performance? Consider These Points:
- Are you experiencing challenges with IO assignmentaccuracy or complex logic development?
- Is your team confident in executing thorough hot and cold loop checkingprocedures?
- Do your HMI graphicsprovide intuitive, real-time insights for your operators?
- Are you seeking a reliable partner experienced with robust controllers like Honeywell HC900?
- Is effortless SCADA communicationwith your controllers critical for your operational visibility?
Our Comprehensive Approach to Power Plant Control System Implementation
At iPAC Automation, we follow a rigorous, phased approach to deliver a control system that is robust, efficient and tailored to your power generation plant’s unique requirements. Our services include:
- Detailed Service Steps (incorporating your input):
- 1. In-depth Study of Customer Input & Requirements:Every successful automation project begins with a deep understanding. We conduct a thorough study of customer input, reviewing your existing infrastructure, operational goals and specific challenges to lay a solid foundation for the control system design.
- 2. Precise IO Assignment & Documentation:Based on detailed engineering and your process requirements, our experts meticulously prepare the IO assignment from the customer IO list. This critical step ensures accurate mapping of field instruments to controller inputs/outputs, forming the backbone of your control system architecture.
- 3. Advanced Hardware Installation & Configuration:We handle the professional installation of control system hardware, including robust controllers like the Honeywell HC900 Hybrid Controller, along with essential Analog Input (AI), Analog Output (AO), Digital Input (DI)and Digital Output (DO) cards installation. Our team ensures proper wiring, power distribution and grounding for optimal performance.
- 4. Sophisticated Logic Development (Hybrid Control Designer):Our engineers develop the complex control logic using industry-leading platforms. For the Honeywell HC900 controller, this involves intricate logic development in Hybrid Control Designer. We craft precise algorithms for PID loops, sequence control, interlocksand safety functions, ensuring stable and efficient plant operation.
- 5. Rigorous Hot and Cold Loop Checking:Quality assurance is paramount. We perform exhaustive hot and cold loop checkingprocedures. This involves validating the entire control loop, from the field instrument to the controller and back, ensuring signal integrity, correct wiring and proper calibration before system go-live. This minimizes commissioning time and risks.
- 6. Iterative Logic Modification & Optimization:We believe in collaborative development. Our team performs logic modification as per customer commentsand operational feedback, iteratively refining the system to perfectly match your plant’s operational nuances and optimize control strategies for peak performance.
- 7. Intuitive HMI Graphics Development:User-friendliness is key to efficient operation. We undertake comprehensive HMI (Human Machine Interface)Graphics modification as per customer requirement. This includes designing clear, intuitive and actionable graphical displays for real-time monitoring, alarm management and process control, enhancing operator situational awareness.
- 8. Quick Builder Configuration & Communication Setup:To ensure effortless integration and data flow, we expertly build the Channel, Controller and points in Quick Builder (QDB). This forms the essential link between your controllers and the SCADA system.
- 9. Verifying Logic-Graphics Communication:A critical step before final handover is to check the communication between logic and graphics. This ensures that all operator commands from the HMI correctly trigger actions in the controller logic and all process data from the logic is accurately displayed on the HMI.
- 10. effortless SCADA Point Communication:We establish robust communication of SCADA points of HC900 Controller through the Quick Builder (QDB). This enables your centralized SCADA systemto effectively acquire data, issue commands and provide a holistic view of your power generation plant, facilitating real-time monitoring and advanced analytics.
Technical Expertise Driving Your Power Plant’s Success
- Our specialized knowledge in PLC/DCS systems, including leading platforms like Honeywell HC900, combined with our expertise in SCADA integration, process safety (SIL), Smart Plant Instrumentation (SPI)and comprehensiveE&I services, positions us as your ideal partner for any power generation automation challenge. We ensure effortless interfacing, data historizationand alarm managementfor optimal plant performance.
The iPAC Advantage: Powering Your Progress in Pune & Beyond
- Reliability & Uptime:Our precisely engineered systems significantly reduce unscheduled downtime and improve plant availability.
- Operational Efficiency:Optimized control loops and intelligent automation lead to reduced fuel consumption and higher output.
- Enhanced Safety:Implementation of robust safety systems, adhering to global standards, protects personnel and assets.
- Data-Driven Decisions:Real-time data visibility and comprehensive reporting empower smarter operational and business decisions.
- Local Expertise, Global Standards:As a prominent automation company in Pune, Maharashtra, we offer responsive local support backed by international best practices.
Call to Action:
Ready to Transform Your Power Plant’s Control System?
Platform: Honeywell’s EPKS(R311), Hybrid Control Designer and HC900 Controller